Elevator Maintenance Checklist: What Every Building Owner Should Know
If you own or manage a building, keeping your elevator in top shape isn’t just smart—it’s essential. Elevators aren’t just about convenience; they’re key to safety, accessibility, and meeting code requirements set by agencies like the Texas Department of Public Safety here in San Antonio.
Regular maintenance helps you avoid breakdowns, stay compliant with safety regulations, and catch small problems before they become expensive repairs. More importantly, it keeps your elevator running smoothly and safely for the people who rely on it every day.
At Elevate Enterprises, we know how much is riding on a reliable elevator. That’s why we’ve put together this straightforward checklist to help building owners stay ahead. Whether you oversee a small commercial space or a large multi-story property, this guide will help you protect your equipment, stay within code, and keep things moving.
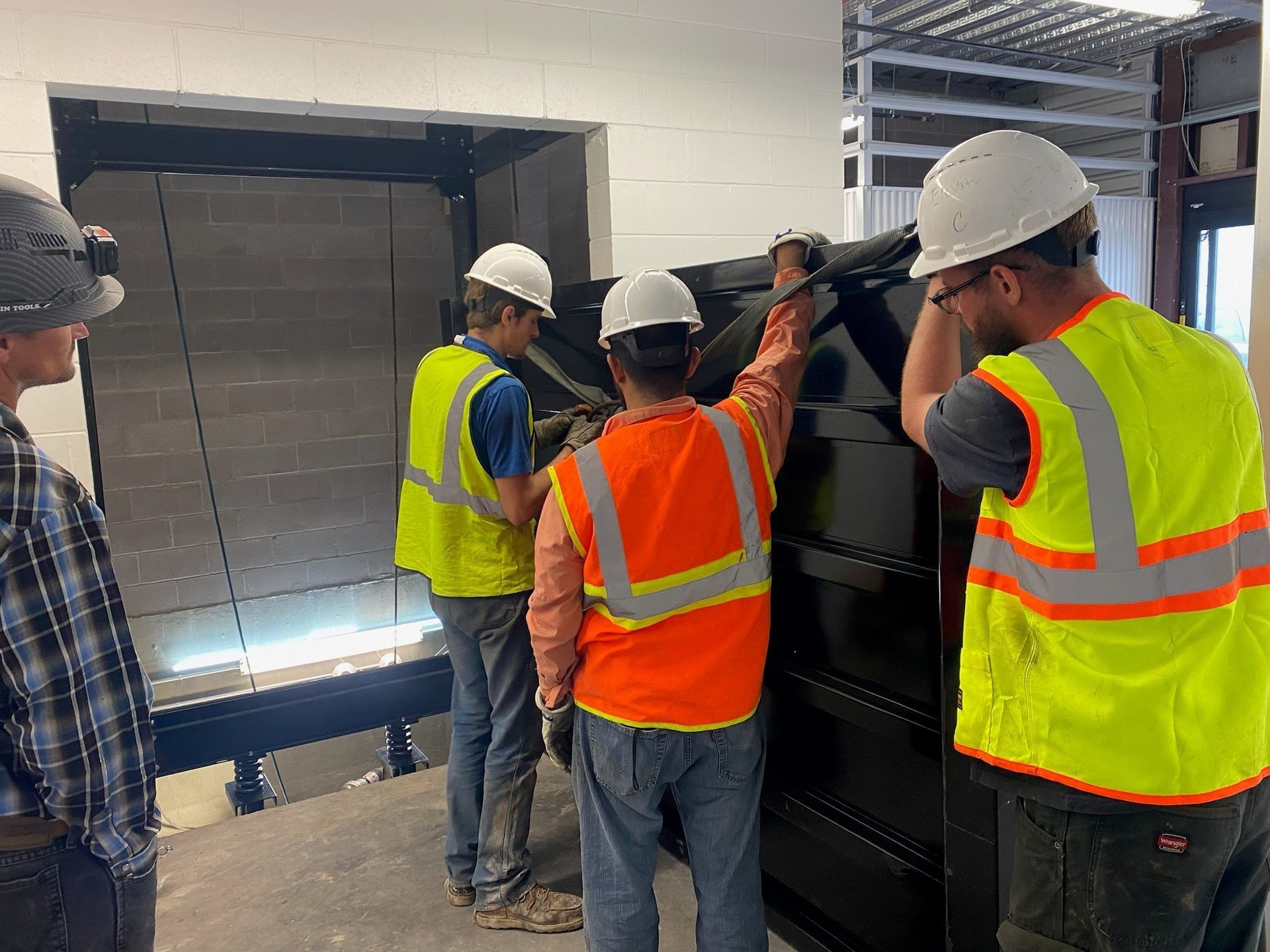
Why Elevator Maintenance is Essential
Elevators move people all day, every day—and when they stop working, it’s more than just an inconvenience. Regular maintenance keeps things running safely, smoothly, and up to code. In San Antonio, the Texas Department of Public Safety keeps a close eye on elevator systems, which makes staying ahead on maintenance even more important.
Here’s why routine service matters:
- Less Downtime – Regular checks help prevent sudden breakdowns that disrupt your building’s flow.
- Fewer Safety Risks – Inspections catch potential hazards before they put passengers in danger.
- Longer System Life – Well-maintained equipment lasts longer and performs better.
- Lower Repair Costs – Spotting issues early can help you avoid expensive emergency fixes.
- Code Compliance – Stay ahead of inspections and avoid penalties with up-to-date maintenance.
Given the complexity of modern elevator systems—many of which now integrate advanced technology such as predictive maintenance software and IoT sensors—it’s crucial to follow a structured maintenance checklist.
The Comprehensive Elevator Maintenance Checklist
Keeping your elevator in good shape takes more than the occasional check-in. Regular, structured maintenance helps you avoid unexpected issues and keeps everything running safely. The checklist below covers the key steps every building should follow—whether it’s handled by your in-house team or a certified elevator technician. Following this guide helps ensure your system stays reliable, compliant, and ready for daily use.
Perform a Visual Inspection
A simple visual check is the first step in spotting early signs of trouble. It doesn’t take long, but it can catch issues before they turn into bigger problems. Here’s what to look at:
- Cab Interior – Look for scuffs, cracks, or damage to the walls, flooring, or ceiling. Make sure the lights are working and that buttons, handrails, and door panels are all secure and in good shape.
- Door Function – Watch the doors open and close a few times. They should move smoothly without jerking or hesitation. If you hear grinding or squeaking, that’s a red flag.
- Call Buttons & Indicators – Test exterior buttons and floor indicators to confirm they light up and respond as expected. Faulty signals can confuse riders and signal a deeper wiring issue.
Inspect the Control System
Elevator control systems are the brains behind the entire operation. Control system failures can lead to misaligned floors, sudden halts, or the elevator failing to start. A regular check of the control systems includes:
- Testing the Control Panel: Ensure that the main control panel is clean, free of dust, and functioning properly. Elevator control systems, such as those used in high-traffic areas in San Antonio, must be tested regularly to meet compliance requirements set forth by local safety regulations.
- Checking Software: Modern elevators often rely on software systems to manage operations. Ensure that the software is up to date and properly calibrated.
Lubricate Moving Parts
Elevators consist of numerous mechanical parts that must be well-lubricated to prevent wear and tear. Failure to maintain adequate lubrication can result in friction, which may cause parts to break down prematurely.
- Shaft and Hoist Mechanisms: Apply lubricant to pulleys, sheaves, and cables to reduce friction and wear.
- Door Operators: Ensure that all moving parts in the door operation system are well-lubricated to prevent them from sticking or grinding.
Test the Brakes
Elevator brakes aren’t something you can afford to overlook. They’re the last line of defense in an emergency, and they need to be in top shape at all times. During maintenance, be sure to:
- Check the Brake Pads – Look for uneven wear, cracks, or thinning. Worn pads can reduce stopping power and need to be swapped out right away.
- Verify the Emergency Brakes – Confirm the system engages properly and brings the cab to a full stop if needed. This isn’t just routine—it’s about keeping passengers safe when it matters most.
Verify Electrical Systems
Elevators depend on a stable electrical supply to operate safely. Even a small issue with wiring or power can lead to shutdowns or unsafe conditions. As part of routine maintenance, make sure to:
- Check Circuit Breakers – Test all breakers tied to the elevator system. They should function properly and show no signs of tripping under normal load.
- Test Backup Power – If your building has a generator or battery backup, verify that it kicks in and keeps the elevator running during an outage.
- Inspect Wiring – Look for frayed wires, loose connections, or any signs of corrosion. Electrical wear can lead to short circuits or unreliable performance.
Perform Load Testing
Load testing is an important part of elevator maintenance to ensure that your elevator can handle the maximum capacity specified by the manufacturer. Regular load testing helps identify any stress points or issues that may arise when the elevator is operating at full capacity.
- Static Load Test: Simulate the maximum capacity weight and observe the elevator’s performance.
- Dynamic Load Test: Run the elevator under full load in real-world conditions, like during peak hours. This helps spot problems that might not show up during regular inspections.
Inspect and Test Safety Systems
Safety features aren’t optional—they’re what protect passengers in emergency situations. That’s why every component needs to be checked and tested regularly. Here’s what to focus on:
- Emergency Alarm – Press the alarm button inside the cab to confirm it activates properly. In San Antonio, elevators must tie into the building’s fire alarm system to meet code, so this connection also needs to be verified.
- Communication System – Pick up the emergency phone or test the intercom to make sure it connects to the right contact—whether that’s building staff or emergency responders.
- Fire Alarm Integration – Make sure the elevator responds correctly when the building’s fire alarm is triggered. It should return to the designated floor and shut down as required by local safety codes.
Review the Elevator’s Performance Data
If your elevator system includes predictive maintenance software, take advantage of it. The data it collects can help you catch small issues before they turn into costly repairs. Here’s what to keep an eye on:
- Usage Stats – Track how often the elevator runs. Heavy use can speed up wear on key components, so high-traffic systems may need more frequent service.
- Error Logs – Look through any alerts or error codes. Patterns or repeat issues in the logs can point to deeper mechanical or electrical problems.
- Energy Use – Keep an eye on power consumption. If usage suddenly spikes, it could mean the system isn’t running as efficiently as it should.
How Often Should Elevators Be Maintained?
While elevators require regular maintenance, the frequency of inspections and servicing can differ due to various factors:
Building Size and Usage
How often your elevator needs service depends a lot on the type of building and how much the elevator is used. In busy high-rises or buildings with constant foot traffic, monthly maintenance is usually the smart call to keep things safe and running smoothly. Smaller buildings with lighter use can often get by with quarterly inspections. Matching your maintenance schedule to how the elevator is used helps prevent wear, reduce downtime, and extend the system’s life.
Age of the Elevator
As elevators get older, they naturally need more attention. Parts wear out, systems slow down, and the risk of malfunctions increases. That’s why older units benefit from more frequent inspections. Routine checks help catch issues early—before they turn into major repairs—and keep the elevator running safely and reliably, even as the equipment ages.
Manufacturer Recommendations
Every elevator is built a little differently, which is why it’s important to stick to the maintenance schedule laid out by the manufacturer. These guidelines are based on the design, components, and expected wear of your specific model. Following them helps keep your system running smoothly, ensures safety, and protects your warranty. From inspection timelines to lubrication and part replacements, the manufacturer’s specs are there for a reason—and skipping them can lead to bigger problems down the line.
The Importance of Hiring Certified Professionals
Elevators aren’t something you can afford to guess your way through. While routine cleaning or quick visual checks might be handled in-house, the real work—inspections, adjustments, and repairs—needs to be done by certified professionals. These systems are complex, and when something goes wrong, the risks are serious. It takes proper training and experience to service them safely and correctly.
Bringing in a licensed provider like Elevate Enterprises means the job gets done safely and by the book. In San Antonio, safety regulations are strict, and failing to meet them can cost you in fines—or worse, put people at risk. Our certified technicians know the local codes inside and out, and they make sure your elevator stays compliant, safe, and running smoothly.
Even elevators in smaller or lower-traffic buildings benefit from routine professional maintenance—usually on a quarterly basis. Combine that with the manufacturer’s recommendations and local safety requirements, and you’re protecting your investment for the long haul.
What are the most common issues found during elevator maintenance?
Some of the problems we see most often include worn cables, door sensors that don’t respond properly, and outdated software that affects performance. On the electrical side, faulty wiring or tripped breakers are common culprits. Regular maintenance helps spot these issues early—before they turn into major repairs—and keeps the elevator running safely and reliably.
Can I perform elevator maintenance myself?
Though routine tasks like cleaning and visual inspections can be done in-house, technical maintenance requires certified professionals. Elevator systems are complex and require specialized tools and training to ensure safety and regulatory compliance. Hiring a licensed technician reduces the risk of accidents and helps prolong the system's lifespan.
What safety features should be regularly tested?
Key safety features include emergency alarms, fire alarm integration, and communication systems like intercoms or phones. Brakes, door sensors, and emergency stop buttons must also be inspected regularly. Testing these features ensures that passengers can rely on the elevator during emergencies and that the system meets safety standards.
Schedule Your Elevator Inspection & Maintenance Today!
Don’t let small issues turn into costly repairs. Ensure compliance with San Antonio’s regulations and protect your building from fines and safety risks.
📞
Contact us today
for a free consultation and a customized maintenance plan to keep your elevators running safely and efficiently!